Ensuring consistency in quality and finish across diverse furniture designs and styles within a panel furniture production line involves several key strategies:
- Standardized Processes: Establishing standardized procedures for each stage of production, including cutting, shaping, assembly, finishing, and quality checks, ensures consistency in operations.
- Quality Control Measures: Implementing rigorous quality control checks at multiple checkpoints within the production line helps identify and rectify deviations from quality standards.
- Material Selection and Handling: Using consistent and high-quality materials and handling them consistently across different designs ensures uniformity in the finished products.
- Precision Machinery and Tools: Employing advanced and precise machinery equipped with appropriate tools ensures consistent and accurate cutting, shaping, and drilling for various designs.
- Templates and Jigs: Creating and utilizing templates, jigs, or fixtures designed for specific furniture designs aids in maintaining consistency in critical dimensions and features.
- Skilled Workforce and Training: Providing comprehensive training to workers ensures they understand and follow standardized procedures, fostering consistency in craftsmanship.
- Optimized Workflow: Organizing the production line layout to optimize workflow and minimize variation in processes helps maintain consistency in the assembly and finishing stages.
- Feedback Mechanisms: Encouraging feedback loops and communication between different production stages allows for continuous improvement and ensures adherence to quality standards.
- Prototype Testing and Approval: Testing prototypes of new designs and obtaining approval before full-scale production ensures that quality and finish meet specified standards.
- Continuous Monitoring and Improvement: Regularly monitoring production metrics, analyzing deviations, and implementing corrective actions ensure continuous improvement and consistency.
By integrating these strategies into the production line’s operations, manufacturers can achieve a high level of consistency in quality and finish across a diverse range of furniture designs and styles, meeting customer expectations and maintaining brand standards.
How does a panel furniture production line handle the integration of different materials, such as wood, glass, or metal, in creating composite furniture pieces?
Integrating different materials like wood, glass, and metal in composite furniture pieces within a panel furniture production line involves specific processes and considerations:
- Design and Planning: The design phase involves careful consideration of how various materials will integrate into the furniture piece. CAD software and mock-ups help visualize and plan the integration.
- Material Compatibility: Understanding the properties and characteristics of each material is crucial to ensure compatibility and structural integrity in the final piece.
- Cutting and Shaping: Machinery equipped with specialized tools and cutting techniques is used to cut and shape different materials according to design specifications.
- Joinery and Assembly Techniques: Specific joinery methods and assembly techniques, Panel Furniture Production Line factory such as doweling, tongue and groove, or adhesive bonding, are employed to seamlessly integrate different materials.
- Adhesives and Fasteners: Selection of appropriate adhesives or fasteners suited for bonding different materials together is essential for durable and stable construction.
- Precision Drilling and Machining: Machinery capable of precise drilling and machining ensures accurate fitting of different materials and components during assembly.
- Handling Fragile Materials: Glass requires careful handling to prevent breakage. Protective measures and specialized equipment are employed to handle and install glass components safely.
- Surface Finishing and Treatment: Different materials may require specific surface treatments or finishes to achieve uniformity in appearance while preserving their individual characteristics.
- Quality Control and Testing: Rigorous quality checks and testing are performed throughout the integration process to ensure structural stability, safety, and overall quality.
- Logistics and Packaging: Special attention is given to packaging and shipping methods to protect delicate materials like glass and ensure the safe transport of composite furniture pieces.
Successfully integrating diverse materials in composite furniture pieces requires expertise in handling different materials, specialized machinery, precision in assembly techniques, and meticulous quality control measures. Collaboration between designers, craftsmen, and engineers ensures the harmonious integration of materials to create functional and aesthetically pleasing composite furniture.
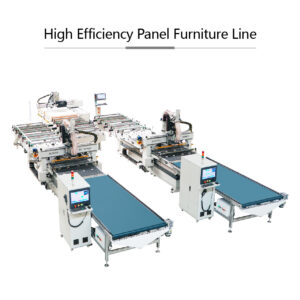