The demolding and stacking process in block machinery involves several steps and mechanisms to efficiently remove cured blocks from the molds and arrange them into stacks for further handling or transportation.
Here’s how it typically works:
- Demolding Mechanism: Block machinery is equipped with demolding mechanisms that release the cured blocks from the molds once they have reached the desired level of curing or hardening. This mechanism may consist of hydraulic cylinders, pneumatic actuators, or mechanical arms that apply force to separate the blocks from the mold cavities.
- Release Agent Application: Prior to demolding, a release agent may be applied to the interior surfaces of the mold cavities to prevent the cured blocks from sticking to the mold. This helps facilitate the demolding process and ensures that the blocks are removed cleanly without damage.
- Vibration or Tapping: In some cases, the block machinery may employ vibration or tapping mechanisms to help loosen the cured blocks from the mold cavities before demolding. Vibrators or pneumatic hammers may be used to impart mechanical energy to the molds, aiding in the release of the blocks.
- Conveyor Systems: Once demolded, the cured blocks are typically conveyed away from the molding area using conveyor systems. These conveyors may be belt conveyors, roller conveyors, or automated transfer systems that transport the blocks to the stacking area.
- Stacking Mechanism: Block machinery may incorporate stacking mechanisms to arrange the demolded blocks into neat stacks for storage or transportation. This stacking mechanism may consist of robotic arms, block machinery gantry systems, or other automated devices that lift and place the blocks into predefined stack configurations.
- Stacking Patterns: Depending on the desired stacking pattern or arrangement, the stacking mechanism can be programmed to arrange the blocks in specific configurations, such as straight stacks, offset stacks, or interlocking patterns. This flexibility allows for efficient use of space and optimized stacking for transportation or storage.
- Control System: The demolding and stacking process is typically controlled by a centralized control system that coordinates the operation of various components and mechanisms. This control system may utilize programmable logic controllers (PLCs), human-machine interfaces (HMIs), or other automation technologies to sequence the demolding and stacking operations accurately.
- Safety Features: Safety features such as interlocks, guards, and sensors are integrated into the machinery to ensure safe operation during demolding and stacking. These features help prevent accidents, injuries, or damage to equipment and personnel.
Overall, the demolding and stacking process in block machinery is carefully engineered to efficiently handle cured blocks and arrange them into stacks for further processing or transportation. By integrating demolding mechanisms, conveyor systems, stacking mechanisms, and control systems, block machinery can automate these tasks and streamline production processes for enhanced efficiency and productivity.
What is the power consumption of the block making machine?
The power consumption of a block making machine can vary depending on several factors, block making machine including the size and capacity of the machine, the type of blocks being produced, the production rate, and the specific features and components of the machine.
Here are some factors that can influence the power consumption of a block making machine:
- Machine Size and Capacity: Larger and more powerful block making machines typically consume more power than smaller machines due to the increased size of motors, hydraulic systems, and other components.
- Motor Power: The power rating of the motors used in the block making machine, including those for the main drive, hydraulic system, conveyor belts, and other auxiliary functions, will directly impact power consumption.
- Production Rate: The rate at which the machine produces blocks affects its power consumption. Machines that operate continuously or at high speeds may consume more power than those that operate intermittently or at lower speeds.
- Operating Voltage: The voltage at which the machine operates will affect its power consumption. Machines operating at higher voltages may consume less power due to reduced electrical losses in transmission and distribution.
- Efficiency of Components: The efficiency of various components within the machine, block making machines for sale such as motors, pumps, valves, and control systems, will influence overall power consumption. Higher efficiency components will generally consume less power to achieve the same output.
- Process Control and Automation: Machines equipped with advanced process control and automation features may optimize energy usage and reduce power consumption by adjusting operating parameters based on real-time conditions and requirements.
- Energy Recovery Systems: Some modern block making machines may incorporate energy recovery systems that capture and reuse energy from certain processes, such as braking or deceleration of moving parts, to reduce overall power consumption.
- Operating Conditions: Environmental factors such as ambient temperature, humidity, and altitude can affect the efficiency and power consumption of the machine’s components. Machines operating under extreme conditions may require additional power to maintain performance.
It’s essential to consult the manufacturer’s specifications and technical documentation for specific details on the power consumption of a particular block making machine model. Additionally, conducting energy audits and monitoring power usage during operation can help identify opportunities for optimizing energy efficiency and reducing overall power consumption in block production processes.
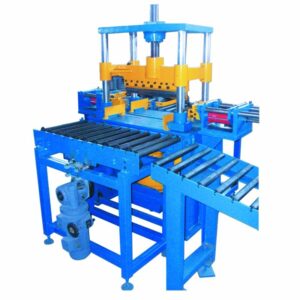