flash point tester
What role does power factor correction play in optimizing the performance of a protection relay testing?
Power factor correction (PFC) plays a significant role in optimizing the performance of protection relay testing in several ways:
- Improved Accuracy: PFC ensures that the power supply provides a near-unity power factor, minimizing reactive power consumption and maximizing the efficiency of energy transfer. This results in a more accurate and reliable testing environment, allowing protection relays to operate under conditions closely resembling real-world scenarios.
- Stable Voltage Supply: PFC helps maintain a stable voltage supply to the protection relays under test by reducing voltage fluctuations and harmonic distortion. A stable voltage supply is essential for accurate relay operation and ensures consistent test results across different testing conditions.
- Reduced Testing Time: By minimizing reactive power consumption and optimizing power delivery, PFC enables faster testing cycles and reduces overall testing time. This is especially beneficial when testing multiple protection relays or conducting routine maintenance tasks, improving productivity and efficiency.
- Prevention of Voltage Sag: Voltage sags or dips in the power supply can affect the performance of protection relays and lead to false tripping or failure to operate under fault conditions. protection relay testing PFC helps mitigate voltage sag by maintaining voltage stability and ensuring adequate voltage levels during testing, enhancing the reliability and effectiveness of protection relay testing.
- Minimization of Heat Generation: Reactive power consumption results in additional losses and heat generation in electrical components, including protection relays and associated test equipment. PFC reduces reactive power flow, minimizing heat generation and extending the lifespan of equipment while improving overall system efficiency.
- Compliance with Standards: Many industry standards and guidelines recommend or require power factor correction for protection relay testing to ensure accurate and reliable test results. Compliance with these standards helps validate the performance of protection relays and ensures the safety and reliability of electrical systems.
- Optimized Energy Efficiency: By optimizing power delivery and minimizing losses, PFC contributes to improved energy efficiency in protection relay testing operations. This is particularly important in applications where energy consumption is a significant concern, such as large-scale relay testing facilities or testing conducted in remote locations with limited power resources.
Overall, power factor correction plays a crucial role in optimizing the performance of protection relay testing by improving accuracy, stability, efficiency, and reliability while reducing testing time, energy consumption, and equipment wear. Implementing PFC ensures that protection relays are tested under optimal conditions, leading to more accurate and dependable operation in real-world applications.

How does the design of a hv testing equipment affect its performance?
The design of high-voltage (HV) testing equipment significantly impacts its performance in terms of accuracy, reliability, safety, efficiency, and overall effectiveness.
Here’s how different aspects of design influence the performance of HV testing equipment:
- Voltage and Current Ratings: The design must accommodate the required voltage and current levels for testing HV equipment. The capability to generate and withstand high voltages and currents ensures compatibility with a wide range of testing applications and equipment.
- Accuracy and Precision: Precise measurement and control of voltage, current, and other electrical parameters are critical for accurate testing results. The design should incorporate high-quality components, calibration procedures, and signal conditioning techniques to minimize errors and uncertainties in measurements.
- Safety Features: Safety is paramount when working with HV equipment. The design should include safety features such as insulation barriers, protective enclosures, interlocks, and grounding systems to prevent electric shock, arc flash, and other hazards to operators and surrounding equipment.
- Reliability and Durability: HV testing equipment must be robust and reliable to withstand the harsh operating conditions encountered in HV testing environments. Rugged construction, high-quality materials, hv testing equipment and thorough testing and validation procedures contribute to the reliability and longevity of the equipment.
- Efficiency and Performance: The design should optimize efficiency and performance to ensure fast and reliable testing operations. Factors such as response time, cooling efficiency, power consumption, and testing throughput all contribute to overall efficiency and effectiveness.
- Flexibility and Versatility: HV testing equipment should offer flexibility and versatility to accommodate different types of tests, equipment, and applications. Adjustable parameters, interchangeable test modules, and customizable test sequences enable adaptation to diverse testing scenarios and requirements.
- User Interface and Controls: The design of the user interface and controls should be intuitive and user-friendly, allowing operators to easily set up tests, monitor results, and navigate menus. Clear displays, tactile feedback, and ergonomic layouts enhance usability and reduce the risk of user errors.
- Integration with Test Systems: Many HV testing applications require integration with other test equipment, data acquisition systems, and automation platforms. The design should support standardized communication protocols, software interfaces, and hardware compatibility to enable seamless integration and interoperability.
- Calibration and Maintenance: Regular calibration and maintenance are essential to ensure the accuracy and reliability of HV testing equipment. The design should facilitate calibration procedures and provide easy access to serviceable components to minimize downtime and maintenance costs.
By carefully considering these aspects of design, manufacturers can develop HV testing equipment that delivers superior performance, reliability, safety, and efficiency for a wide range of testing applications in industries such as power generation, transmission, distribution, aerospace, automotive, and manufacturing.

How do wet wipes for babies websites cater to different needs and preferences?
Wet wipes for babies websites cater to different needs and preferences in several ways to ensure that they meet the diverse requirements of parents and caregivers.
Here are some common strategies:
- Variety of Products: These websites offer a wide range of wet wipes products designed for different purposes, including diaper changes, hand and face cleaning, and general hygiene. Products may vary in size, thickness, fragrance, and ingredients to accommodate different preferences.
- Sensitive Skin Options: Many websites offer wet wipes specifically formulated for babies with sensitive skin. These wipes are often hypoallergenic, fragrance-free, and free from harsh chemicals or irritants that may cause skin irritation or allergies.
- Different Pack Sizes: Wet wipes websites typically offer different pack sizes to accommodate varying usage needs and preferences. Customers can choose from travel-sized packs for on-the-go convenience, bulk packs for cost savings, or individually wrapped wipes for added hygiene.
- Eco-Friendly Options: Some websites offer eco-friendly wet wipes made from biodegradable materials or sustainable fibers. These wipes appeal to environmentally conscious parents who prefer products that are gentle on the planet.
- Specialized Formulas: Websites may offer wet wipes with specialized formulas targeting specific concerns, such as extra moisturizing wipes for dry skin, antibacterial wipes for added hygiene, or soothing wipes for diaper rash relief.
- Customization Options: Some websites allow customers to personalize their wet wipes by choosing custom packaging designs, adding names or messages, or selecting specific scents or ingredients. wet wipes for babies This customization adds a personal touch and makes the wipes unique to each customer.
- Subscription Services: Many wet wipes websites offer subscription services that allow customers to receive regular deliveries of wet wipes at scheduled intervals. This convenient option ensures that parents never run out of wipes and can save time and effort by automating their purchases.
- Educational Content: Websites may provide educational content, such as articles, guides, and videos, that offer tips and advice on baby care, diapering, and using wet wipes safely and effectively. This information helps parents make informed decisions and feel confident in their choices.
- Customer Reviews and Ratings: Wet wipes websites often feature customer reviews and ratings for their products, allowing prospective buyers to read about other parents’ experiences and feedback. This helps customers gauge the effectiveness, quality, and suitability of the wipes for their needs.
By offering a diverse range of products, customization options, eco-friendly choices, and educational resources, wet wipes for babies websites cater to different needs and preferences, ensuring that parents can find the right wipes for their little ones.
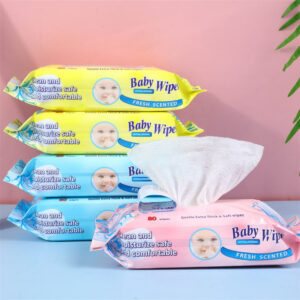
How do custom wet wipes websites ensure the security of online transactions?
Custom wet wipes websites prioritize the security of online transactions by implementing various measures to protect sensitive information and prevent unauthorized access. Here are some common practices:
- Secure Socket Layer (SSL) Encryption: Websites use SSL encryption to secure data transmitted between the user’s browser and the website’s server during online transactions. This encryption ensures that sensitive information, such as credit card details and personal data, is protected from interception by unauthorized parties.
- Payment Gateway Integration: Custom wet wipes websites integrate with trusted payment gateways that comply with Payment Card Industry Data Security Standard (PCI DSS) requirements. These payment gateways use advanced security protocols to process transactions securely and protect payment information.
- Tokenization: Some websites implement tokenization, a process where sensitive payment data is replaced with a unique token. This token is used to represent the payment information during transactions, custom wet wipes reducing the risk of exposing sensitive data in the event of a security breach.
- Two-Factor Authentication (2FA): Websites may offer two-factor authentication as an additional layer of security for user accounts. This requires users to provide a second form of authentication, such as a unique code sent to their mobile device, in addition to their password, to access their account or complete transactions.
- Fraud Detection Systems: Websites employ fraud detection systems that monitor transactions for suspicious activity, such as unusual purchase patterns or multiple failed login attempts. These systems help identify and prevent fraudulent transactions, protecting both the website and its customers.
- Secure Hosting Environment: Websites are hosted on secure servers with robust security measures in place to prevent unauthorized access and data breaches. This includes regular security updates, firewalls, intrusion detection systems, and data encryption protocols.
- Regular Security Audits: Websites conduct regular security audits and vulnerability assessments to identify and address potential security risks. This includes testing for vulnerabilities in the website’s code, infrastructure, and third-party integrations.
- Privacy Policy and Terms of Service: Websites have clear and transparent privacy policies and terms of service that outline how customer data is collected, used, and protected. This provides transparency and reassurance to customers about the security of their information.
- User Education: Websites educate users about best practices for online security, such as creating strong passwords, avoiding public Wi-Fi for sensitive transactions, and recognizing phishing attempts. This helps empower users to protect themselves from potential security threats.
By implementing these security measures, custom wet wipes websites help ensure the security of online transactions and provide a safe and trustworthy shopping experience for their customers.

Portable Wet Wipes Making Machine
ZY series wet wipes production line is used to produce disposable household cleaning wet wipes or baby wipes. Fully automatic wet towel production equipment can meet the needs of enterprises for high production capacity, and multiple models of products can be selected, with production capacity of 400pcs/min- 16000pcs/min; Packing: 10pcs/bag-80pcs/bag, large cloth cutting range with large throwing knife, automatic connection between cloth placing frame and film placing shaft, reduced time for replacing raw materials, and effectively improved working efficiency; On-line inspection of cloth joints and on-line removal of connection joints ensure the quality of products.
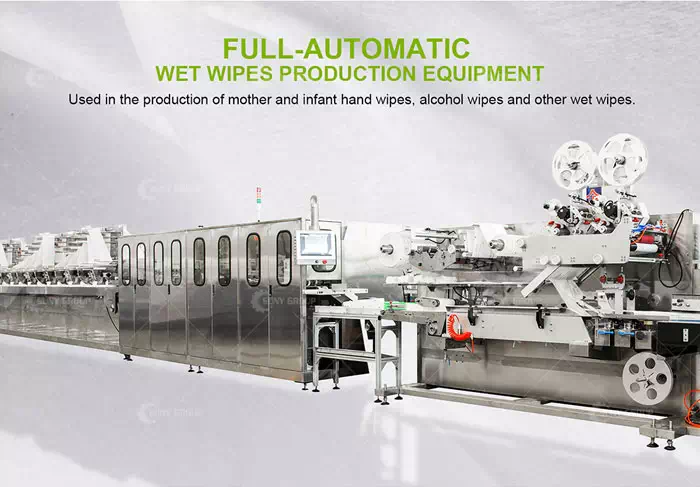
APPLICABL EMATERIALS:
Spunlace nonwoven,Hot rolled fabric,degradable non-woven fabrics,wet strength paper etc.Specification nonwovens Max width is 1 200mm, two independent rolls in one reel shaft..
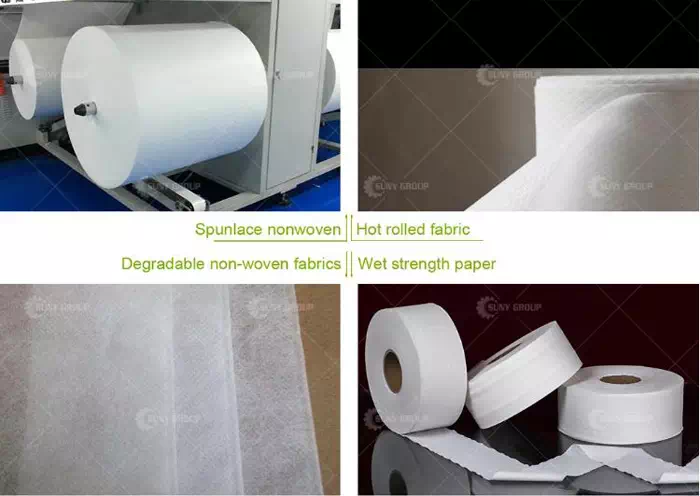
Applicable packing materials: PET/PE BOPP PET/AL/PE and other hot sealable materials Film rolling speification: Max width is 420mm, diameter is 360mm. Applicable labels: transparent labels & non-transparent labels; Metal labels are optional; Label speification: Max W100mm,φ400mm 2-axis labels are prepared.
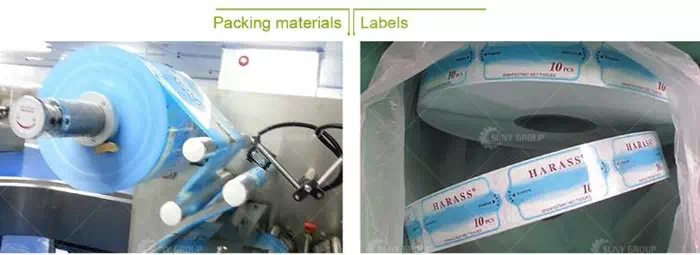
WET WIPES TYPE:
Wet tissue equipment is used to produce baby wipes, disinfected wet wipes, cleaning wet wipes and other types of wet wipes, wet wipes folding method, a pack of quantity, opening method etc., can be customized and adjusted.
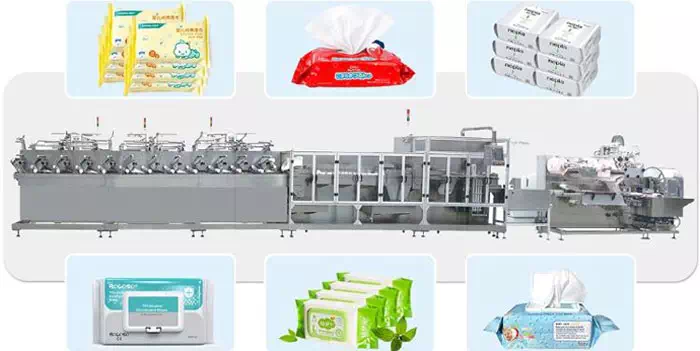
How does the making mini wet wipes machine handle changes in the level of automation or manual intervention?
The mini wet wipes making machine can handle changes in the level of automation or manual intervention through several means:
- Adjustable Settings: The machine may have adjustable settings that allow operators to customize the level of automation according to production requirements. This could include settings for the speed of production, the degree of automation in certain processes, and the level of operator involvement.
- Modular Design: A modular design allows for flexibility in the machine’s configuration, enabling easy integration or removal of automation components as needed. This allows operators to adapt the machine to different production scenarios without major reconfiguration.
- Manual Override Controls: The machine may be equipped with manual override controls that enable operators to intervene in the production process when necessary. This could include manual controls for individual machine functions or emergency stop buttons for halting production.
- Automation Sensors: Automation sensors integrated into the machine monitor various parameters such as material supply levels, machine performance, and product quality. These sensors provide real-time feedback to the control system, allowing for automatic adjustments in production settings based on changing conditions.
- User Interface: An intuitive user interface facilitates interaction between operators and the machine, allowing for easy adjustment of settings and monitoring of production status. This interface may include touchscreen displays, making mini wet wipes machine control panels, and visual indicators to communicate information effectively.
- Remote Monitoring and Control: Some machines offer remote monitoring and control capabilities, allowing operators to oversee production activities from a distance. This feature enables operators to adjust machine settings, troubleshoot issues, and intervene when necessary without being physically present at the machine.
- Training and Support: Comprehensive training and support are essential for operators to effectively manage changes in automation levels. Proper training equips operators with the skills and knowledge needed to operate the machine efficiently and make informed decisions regarding automation settings.
By incorporating these features and strategies, the mini wet wipes making machine can effectively handle changes in the level of automation or manual intervention, ensuring optimal performance and adaptability to varying production requirements.

How does the machine prevent overfilling or underfilling of wet wipe packs?
The prevention of overfilling or underfilling of wet wipe packs is typically ensured through several mechanisms and controls in the machine’s design and operation:
- Precise Pumping System: The machine may utilize a pumping system calibrated to dispense the exact volume of wet wipe solution needed for each pack. This system ensures consistency in the amount of solution dispensed, preventing overfilling or underfilling.
- Level Sensors: Level sensors are often installed to monitor the amount of solution in the reservoir or dispenser. These sensors trigger the pumping mechanism to stop when the desired level is reached, preventing overfilling.
- Weight or Volume Measurement: Some machines may incorporate weight or volume measurement systems to verify that each pack contains the correct amount of solution. If the measured weight or volume deviates from the set parameters, the machine can adjust the dispensing process accordingly.
- Automated Control Systems: Advanced control systems can regulate the dispensing process in real-time based on preset parameters. These systems can detect and correct deviations from the desired fill level, ensuring consistency across all packs.
- Optical Sensors: Optical sensors may be employed to detect the presence of wet wipes in the packaging assembly. These sensors ensure that the next wet wipe is only dispensed when the previous one is correctly positioned, vertical type single wet wipe machine preventing underfilling due to missing wipes.
- Feedback Mechanisms: The machine may incorporate feedback mechanisms to adjust the dispensing process based on factors such as substrate thickness, speed of production, or viscosity of the solution. This adaptive control helps maintain consistent fill levels regardless of variations in production conditions.
- Calibration and Testing: Regular calibration and testing of the dispensing system are essential to ensure accuracy and consistency. By periodically verifying the machine’s performance against established standards, operators can identify and rectify any issues that may lead to overfilling or underfilling.
By integrating these features and mechanisms into its design, the machine can effectively prevent overfilling or underfilling of wet wipe packs, ensuring product quality and customer satisfaction.

Filter Press Membrane Working Principle
A filter press membrane is a critical component in the separation process of various industrial applications. It plays a vital role in separating particles of different sizes and densities, ensuring the purity and quality of the final product. In this article, we will delve into the working principle of a filter press membrane and explore its importance in various industries.
Working Principle of a Filter Press Membrane
A filter press membrane is essentially a thin, flexible film designed to separate particles based on their size and density. The membrane is made up of a network of tiny pores that allow larger particles to pass through while trapping smaller ones. The pores are typically arranged in a random pattern, providing a high degree of filtration efficiency.
The working principle of a filter press membrane is based on the principle of capillary action. Capillary action refers to the tendency of fluids to flow along the narrowest part of a container, which is the wall of the capillary tube. In the case of a filter press membrane, the pores in the membrane act as the narrowest part of the container, allowing larger particles to pass through while trapping smaller ones.
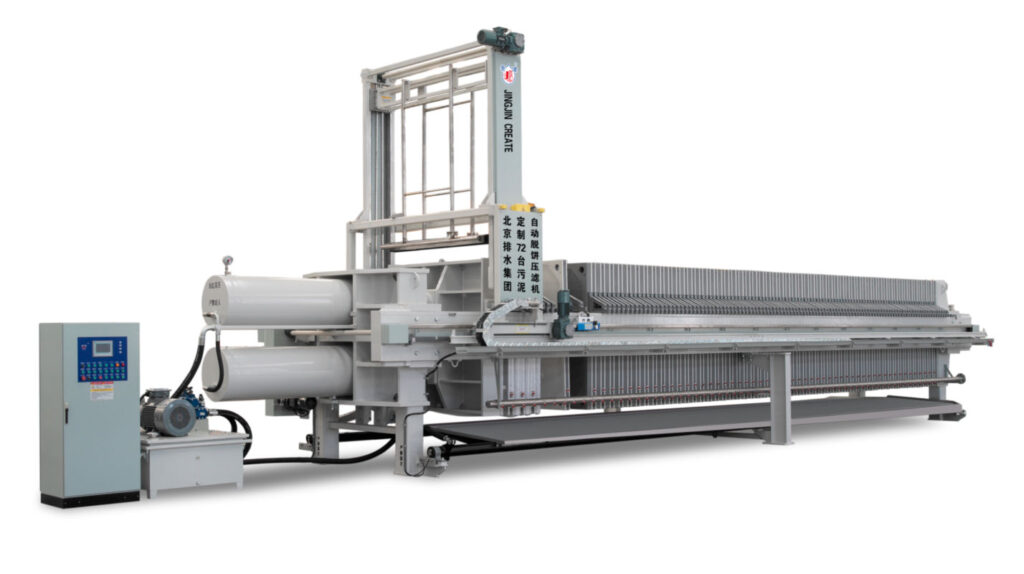
Importance of Filter Press Membranes in Various Industries
Filter press membranes are popular in various industries, including food processing, pharmaceuticals, and mining. In the pharmaceutical industry, filter press membranes are popular in separating active ingredients from impurities. Ensuring the purity and quality of the final product. In the mining industry, filter press membranes are popular in separating gold and other metals from ore. Increasing the yield and profitability of the mining process.
Advantages of Filter Press Membranes
Filter press membranes offer several advantages over other separation techniques. They are highly efficient, with a filtration rate of up to 99%, making them ideal for separating particles of different sizes and densities. They are also highly versatile and capable of separating a wide range of materials, including liquids, powders, and granular materials. Additionally, filter press membranes are relatively low-cost and easy to maintain, making them an attractive option for many industries.
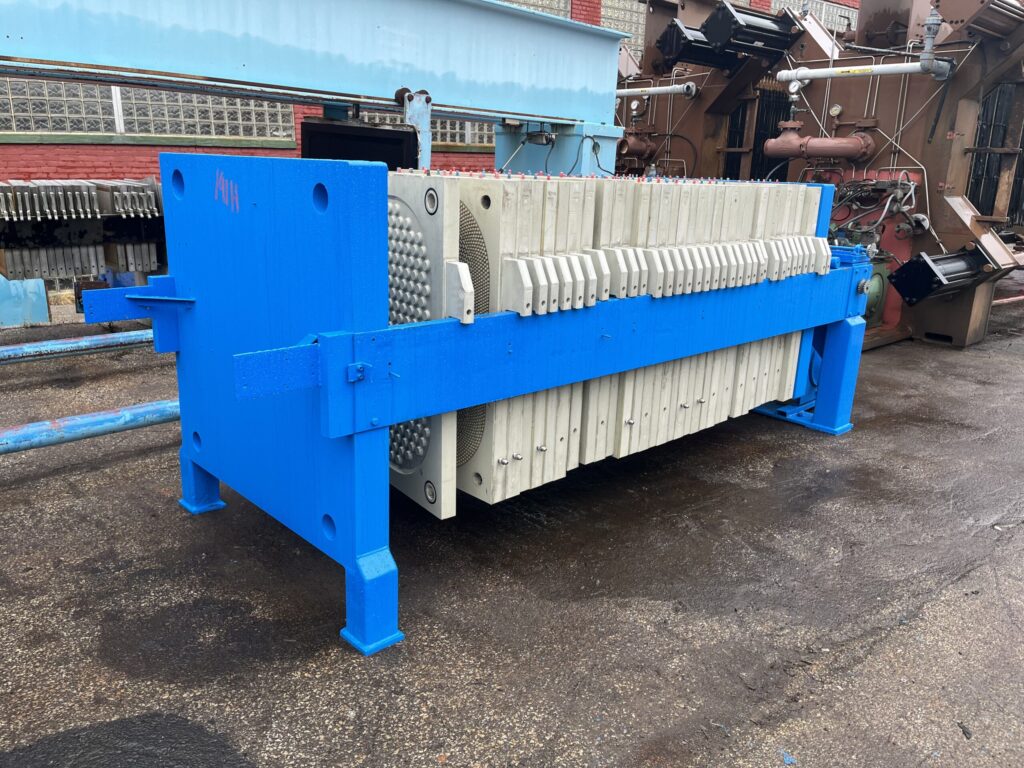
Conclusion
In conclusion, filter press membranes are a critical component in the separation process of various industrial applications. Their working principle is based on the principle of capillary action. Allowing them to separate particles based on their size and density. Filter press membranes offer several advantages over other separation techniques, including high efficiency, versatility, and low cost. They are widely used in industries such as food processing, pharmaceuticals, and mining, and continue to play a vital role in ensuring the purity and quality of our products.
What is the difference between radial and centrifugal fan?
When it comes to industrial fans, you’ll always have a choice among several options. But when selecting fans for a variety of industries — including those for use in mines, factories, and commercial buildings — two of the most popular types are axial and radial.
Not only are axial and radial fans the most applicable across a broad range of industries, but they’re also the two most common types of fans available today on the market.
Industrial Fans: Understanding The Difference Between Axial and Radial Fan
So what type of fan — axial or radial — is better for your application? Neither is a bad choice, but there are situations when one should be selected over the other. Hence, choosing the right type of fan often comes down to factors such as air displacement, volume, and even blade type. This post will take a closer look at the basics, key differences, and advantages and disadvantages of both axial and radial fans.
Axial Fans
If you’ve ever lived in a home without air conditioning or slept in a loft that required a bit more air circulation to promote a comfortable environment, the portable fan that you set up to help cool the area is likely an axial fan.
Axial fans got their name for the way the fan blades operate — rotating around an axis and thereby pushing air out in a way that’s parallel to the axis. The example that we used above is common in household and small industrial settings. However, axial fans can be made much larger, suitable for factories and underground mining operations.
Axial fans are frequently used when there’s a need for a large volume of air. Though axial fans do a nice job achieving this goal, it’s fairly low-pressure air and not highly concentrated to a certain area.
Radial Fans
Also known as “centrifugal fans,” radial fans don’t pull air parallel to the axis as axial fans do. Instead, they move air from the center, radially — hence their name. To create the air, radial fans first pull it into the fan. This is often done via a side intake, which varies based on how the size of the fan.
A simple example of a centrifugal fan is a small “blower” fan, used in residential and commercial environments to quickly dry damp areas of the building or areas with water damage.
Though the volume of these types of fans is usually less than that of axial fans, the pressure is much greater. They’re also better able to directly target a specific area. Radial fans used in heavy industrial and mining environments are typically larger, drawing in the air via intakes and then running it through a series of ducts before it is dispersed.
Centrifugal fans may also be known as squirrel fans, squirrel cage fans, and air blower fans because of how they operate and how certain models look.
